On-Site Fan and Blower Balancing
Fan & Blower Balancing
We offer complete maintenance, troubleshooting, and repair services on most types of industrial fans. We have the knowledge and experience required to troubleshoot and correct all fan problems. We work with fan manufacturers and reps when necessary to provide innovative solutions and quick response to the needs of customers in a wide array of industries.
All fans require regular maintenance to give optimal and dependable service. Proper lubrication and periodic inspection will increase the reliability of your fan and is especially important if a failure can shut down your operation.
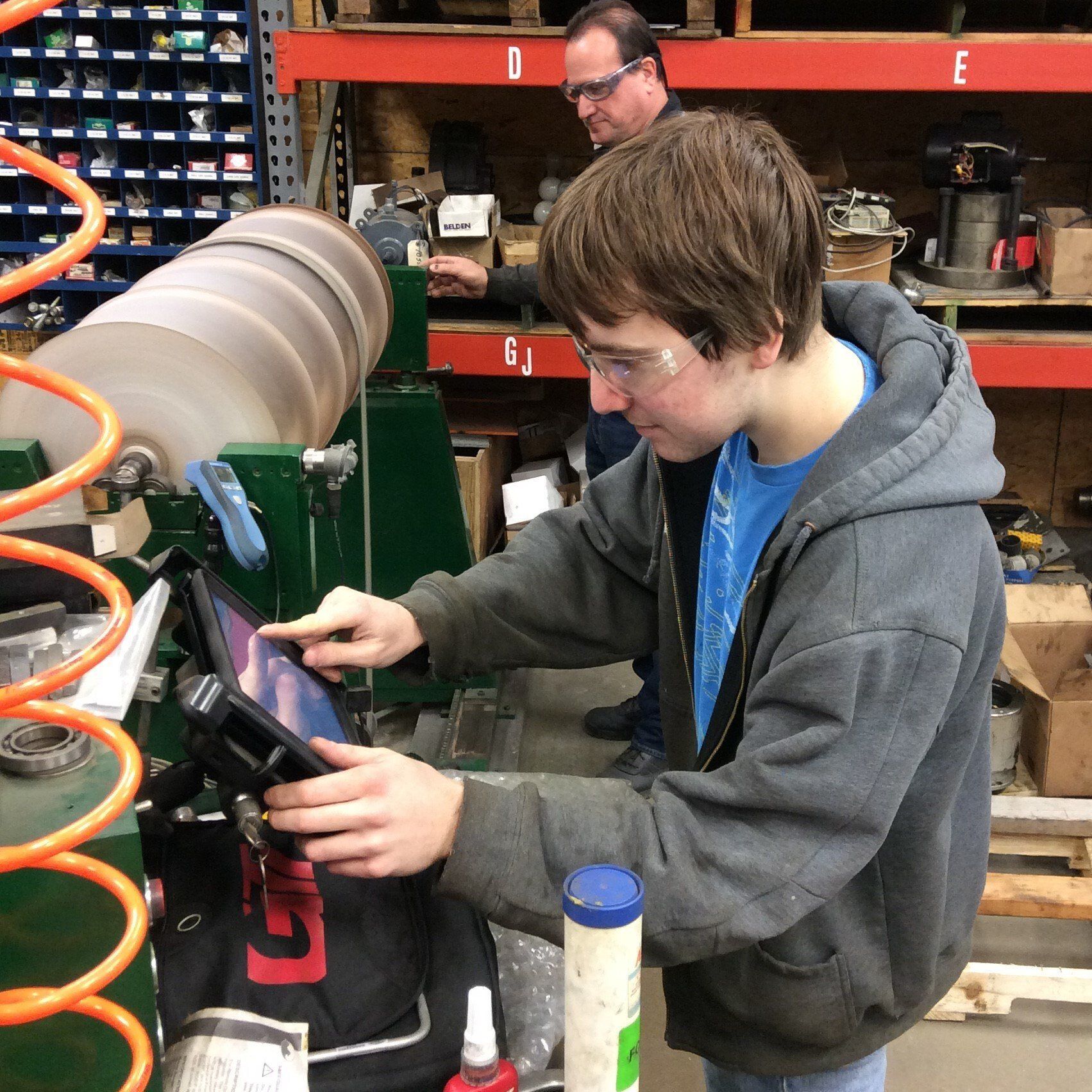
Many times we have seen bearings replaced when the fan becomes noisy – only to find the problem still exists. This is because the problem was not with the bearings themselves, the fan was shaking and noisy because of imbalance. We have the ability to identified and corrected the vibration source and balance the fan blade to OEM specifications. Sometimes the bearings fail because of unbalance and will only fail again prematurely if this condition is not corrected. The noise you hear may be an out of balance condition which can be corrected before damage occurs.
EMX Electro-Mechanical service team has the ability to help you with the reconditioning, repairing, and rebuilding of industrial fans and blowers, including:
- Axial
- Centrifugal
- Squirrel Cage
- Single and Multi-stage blowers
- Air-Handlers (HVAC)
- Cooling Towers
- Induced Draft-ID Fans
- Exhaust
- Positive Displacement Blowers
- Tube axial
- Dust Collection
- Ventilator Fans
Through a variety of tests and assessments, we will have your equipment restored and back in service as quickly as possible – ensuring a short turnaround time and high quality repair.
1. Die-penetrant Test
With a fan running at such a high speed, a die penetrant test uses a die, sprayed on the fan blades to detect a crack. Our team can either repair or recommend the equipment be removed from operation due to safety issues.
2. Shaft Repair
By working with our machine shop to manufacture or repair a shaft used in a fan or blower, customers experience a cost savings since this is more affordable than purchasing from a factory.
3. Fan and Blade Balancing
By reducing the vibration, fan and blade balancing extends the life of your equipment. EMX’ Balancing Systems are designed to perform measurements of vibrations and calculations within horizontal shop balancing machines, and in the field.
4. Housing Inspection and Repair
Cracked equipment causes vibration that leads to inefficient and unsafe operations. with a thorough inspection, Our technicians can detect issues and bring equipment back to its original specifications.
5. Vibration-Analysis
At some time during the life of a fan or blower, it is likely to experience high vibration levels. What’s behind this maintenance phenomenon? The cause may be an electromagnetic or mechanical imbalance, loose components, rubbing parts, bearing failure, or resonance.When a problem occurs, it is critical to quickly identify the source and take corrective action. Using EMX’ latest vibration analysis diagnostic techniques can save you money and downtime. EMX’ uses VibePro 7.3.5 which is a portable device, route-based instrument used for collecting vibration data on rotating machinery. It reduces collection, analysis and reporting time, compared with similar devices. This allows EMX to determine the severity of the stress level of bearing or gear wear on your equipment. The data is recorded from each machine and uploaded on the software, providing quick recognition of change in the vibration pattern, as an indicator of deterioration. Corrective actions are then taken.
EMX Fan and Blower Services
Precision Installation, Maintenance and Repair Service. Emergency Services are available 24 hours a day, 365 days a year.
Dynamic Balancing
EMX Electro-Mechanical’s state of the art Balancing Systems are designed to perform measurements of vibrations and calculations within horizontal shop balancing machines as well as, in the field. The application measures the running speed (1X) filtered vibration amplitude and relative phase with a reference mark in the rotor to allow full balancing correction. All Dynamic Balancing results will be performed to the level specified by the customer. In the absence of a requested level, dynamic balancing to balance quality grade G2.5 (ISO 1940/1) should enable the machine to meet final vibration limits. A Balance weight or weights are secured to rotor and will be located so that they do not interfere with other machine components.
Why Balance?
Rotating components experience significant quality and performance improvements when balanced. Balancing is the process of aligning a principal inertia axis with the geometric axis of rotation through the addition or removal of material. By doing so, the centrifugal forces are reduced, minimizing vibration, noise and associated wear. Virtually all rotating components experience significant improvements when balanced. Balancing can contribute to more efficient, more powerful,quieter, smoother running and longer lasting equipment and is one of the most cost effective means of providing value to our customer.
Think of imbalance as an imaginary heavy spot on a rotating shaft. This heavy spot is pulling the shaft and the center of rotation of the center line off the shaft on every rotation. The force of the imbalance is transferred to the bearing and case of the machine causing heat, friction, lubrication failure, and bearing faults. Extreme imbalance can cause looseness in the machine train. There are many reasons for imbalance to be present in a rotor. Deposit and build-up causes imbalance as deposits of dirt and grime build up on a rotor and its parts over time. The build-up of these deposits may be gradual, but not necessarily equal and can cause an imbalance condition. While the build-up may be gradual, the deposits will break away at an uneven rate causing a more serious imbalance. This can be especially true of fan blades. Fan blades will tend to collect deposits in a linear fashion, but the deposits will not come off at the same rate. They will come off in unequal pieces causing serious imbalance. Make cleaning of rotor, rotating parts and fan blades a regular part of your scheduled inspection and preventative maintenance. Rotors can also be damaged when exposed to abrasive or corrosive materials. This will cause uneven wear and an imbalance condition. When you choose products, make sure their rotors are made from materials that can withstand corrosion and abrasion over long periods of time. Eccentricity exists when the true or geometric centerline of a part does not coincide with its rotating center. This can be a manufacturing defect. Eccentricity can also be caused by out of roundness of the shaft, variations in electrical properties or uneven heating.
Vibration-Analysis
At some time during a motor’s life, it is likely to experience high vibration levels. What’s behind this maintenance phenomenon? The cause may be an electromagnetic or mechanical imbalance, loose components, rubbing parts, bearing failure, or resonance.
When a problem occurs, it is critical to quickly identify the source and take corrective action. Using EMX’ latest vibration analysis diagnostic techniques can save you money and downtime. EMX’ uses VibePro 7.3.5 which is a portable device, route-based instrument used for collecting vibration data on rotating machinery. It reduces collection,analysis and reporting time, compared with similar devices. This allows EMX to determine the severity of the stress level of bearing or gear wear on your motor. The data is recorded from each machine and uploaded on the software, providing quick recognition of change in the vibration pattern, as an indicator of deterioration. Corrective actions are then taken.
Benefits:
Vibration in rotating machinery is commonly the result of mechanical faults including mass unbalance, coupling misalignment, loose components, and many other causes. Improving the levels of vibration should always include elimination of the source of vibration and not addressing the symptom by making balance corrections. Mass unbalance will produce vibration due to the force generated by the eccentric weight. This force will be imposed at the running speed of the shaft, and depends on the amount eccentric mass the eccentricity of the weight , and the frequency of rotation . In more common terms the unbalance is defined by the eccentric weight, mounting radius, and shaft speed. The observed vibration signature will show elevated amplitudes at 1xRPM and no other significant frequencies when rotor unbalanced is the main fault.
Unfortunately, other common faults can also generate high levels of vibration at 1xRPM including coupling misalignment, looseness, rotor bows, and a variety of other sources. In some cases, these faults will produce other symptoms that can suggest corrections other than balancing should be done. Yet in many cases, balancing may be the chosen course of action for lowering vibration amplitudes even though it is not the source of vibration. Once it is determined that balance corrections should be made, the balancing process includes measuring reference vibration, adding trial weights, observing the response due to trial weights, and using the response characteristics to determine the location of balance correction weights to reduce vibration to an acceptable level.
Vibration analysis and trending is a method of evaluating current machine condition and monitoring a machine’s changes over a period of time. It can also be used to pinpoint a source of several problems such as misalignment, imbalance and bearing issues. Vibration Trending and Analysis can be performed on all rotating equipment.
Benefits of Vibration Trending & Analysis
- Diagnose imbalance & misalignment
- Discover bearing issues
- Applicable on any rotating equipment
- Improve equipment reliability and uptime
- Prevent catastrophic failure
- Improve machine safety levels
Applications for Vibration Trending & Analysis
- Motors
- Pumps
- Air handlers
- Fans
- Machines