New Paragraph
Electric Motor Repair & Rewinding
Our goal is to provide you with the best Electric Motor Repair solution possible and the information you need to manage your maintenance and reliability programs. We provide Electric Motor Repair and Rewind and Pump rebuild services through 1,500 HP.
Electromechanex promotes best practice and reliability throughout its business. Quality steps reinforce our procedures, which are based on IEEE, NEMA, and EASA standards. As an EASA Repair Shop, we ensure each and every repair is to the highest specification.
All motors are assembled in accordance with the equipment technical manual, our In-House Motor Repair Specification, and good machine shop practices. By following this repair specification, we ensure motors rebuilt in our shop are, as good as, if not better than new. Further to Electric Motor Repair and Rewind, we also provide Field Service and Predictive Maintenance services including:
Vibration Analysis on motors, bearings and other rotating equipment
Infrared Thermal Inspections of electrical and mechanical systems
Winding Testing and Analysis
Onsite Fan & Blower Balancing and Laser Shaft Alignments
Automation, Drives & PLC Controls
Motor and Pump Installations and monitoring the condition of your unit for reliable long-term operation.
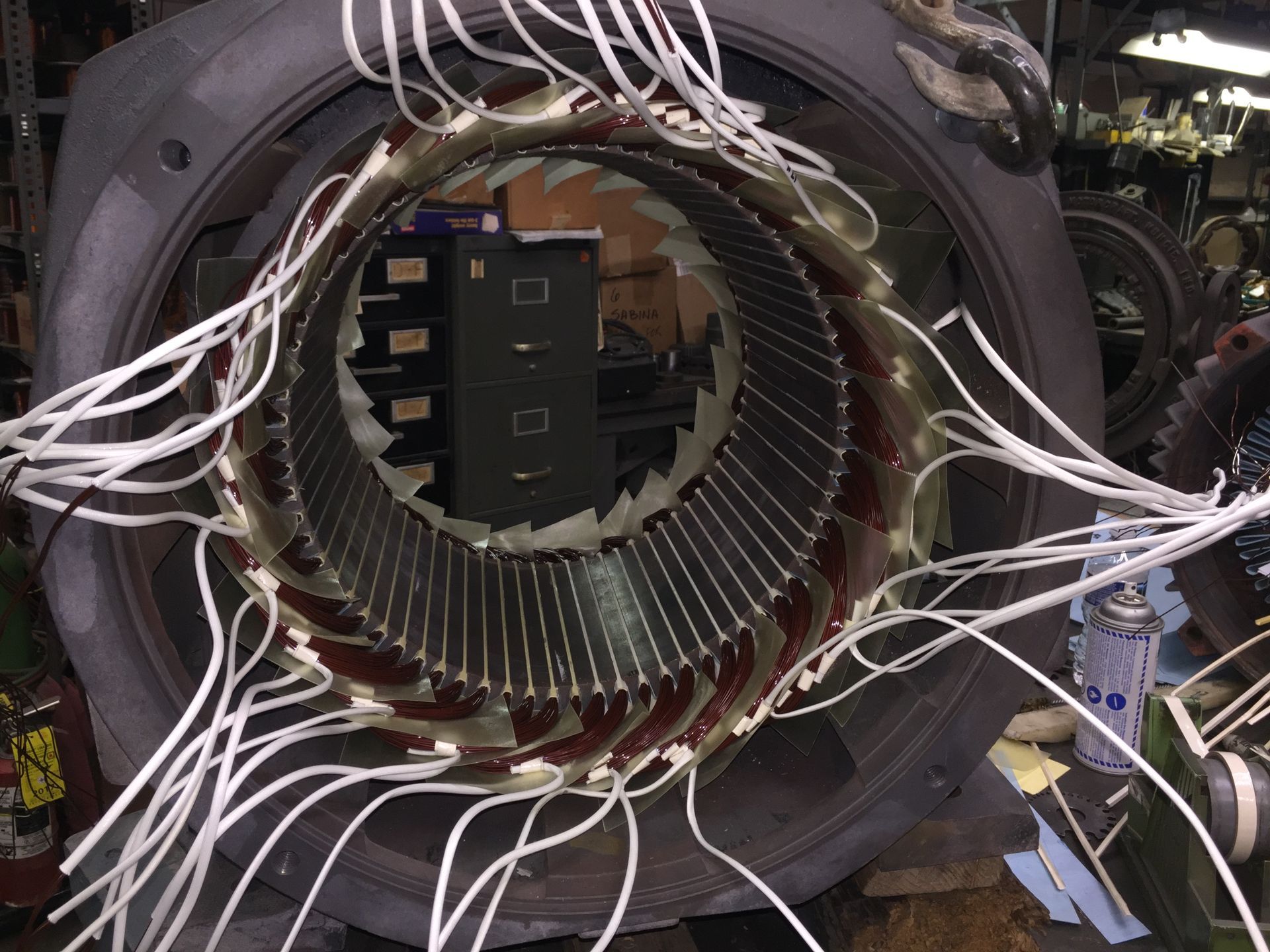
Electric motors are among the highest reliability incident reports for many companies. This leads to a continual cycle of costly electric motor repair, inconsistent quality and unplanned downtime factors that can hurt your bottom line. We not only repair and refurbish your motor but to provide root cause failure analysis on why it has failed. We consistently provide electric motor repairs and refurbishments that are better than new motors!
Our comprehensive Electric Motor Service, repairs motors, when you need them, performed to state-of-the art standards. Shop and Field Service
support capabilities include 24 hour service, 7 days a week, 365 days a Year. #electricmotorrepair #machining #pumprebuilding #pumpexperts #expertservicesolutions #expectthebest24/7 #keepingindustrymoving
OUR REPAIR BENEFITS
- Complete Motor Inspection and Cleaning
- Provide complete failure and documentation to determine the Cause of Motor Failure
- Comprehensive Bearing Inspection and new Bearing Installation
- Digital pictures available for Inspection
- Commissioning of your Equipment
- Non-destructive winding analysis and testing
- All Rewinds are made using Class “H” Insulation & Inverter Duty Wire
- Utilize the best available technology in the repair of your Motor.
- Treat your Motor problems with concern.
Repair Specifications
Model Repair Specifications
Electromechanex promotes best practice and reliability throughout its business.
As an EASA Repair Shop, we ensure each and every repair is to the highest specification technical requirements of ANSI/EASA AR100-2020.
All motors are assembled in accordance with the equipment technical manual and good machine shop practices. By following this repair specification, we ensure motors rebuilt in our shop are, as good as, if not better than new, by enhancing material and process specifications found on standard industry offering AC motors.
We back this up by covering all rewinds with a 2-Year Guarantee.
The intent of the Model Repair Specification is to achieve a consistent, high quality diagnosis, repair and/or overhaul of a motor, and to return it to good operating condition with a minimum of delay and cost. Not all repair situations can be covered in these Model Repair Specifications. In the absence of specific instructions, the requirement shall be to restore the motor to as-manufactured condition.
AC Motor Repair Specification
1.0 INCOMING INSPECTION
EMX Motor Repair Shop performs a thorough appraisal of the motor’s condition, as received, to determine what specific repairs are needed as well as to find unsuspected trouble, perhaps unrelated to the obvious defect. Our technicians diagnose cause and effect to help prevent a recurrence. The motor may have been sent to our Repair Facility with limited external evidence as to the nature and location of trouble. What seems wrong may be correctable in several ways. Our appraisal will include a complete review of the following conditions of each part of the motor: General cleanliness, Cracked or broken welds or castings, Missing hardware, Wear or rub marks, including fretting, discoloration, charring, or other evidence of overheating Looseness at mating fits, Corrosion, moisture, or oil inside the machine. Digital Photographs of any abnormal conditions found are part of the appraisal process and inspection report. Our AC Motor Repair includes dissassembly, detailed inspections, and measurements to identify electrical and mechanical damage.
2.0 INITIAL MOTOR TEST RUN
Prior to an incoming run test, we perform the following and record information where appropriate: Motor will be mechanically inspected to determine if shaft turns freely, Verify that bearings are lubricated, Insulation resistance tests are performed. As well as , the continuity of stator windings, condition and installation of brushes, if applicable, Single-phase, low-voltage test (approximately 10-20% of rated voltage) on AC squirrel-cage rotor to find defective rotor bars, Polarization index (where appropriate). Surge test (where appropriate). If conditions permit, the motor will be run at reduced voltage initially (25-50% of rated voltage). If the test is successful, Results are recorded, and then the motor will be run at full rated voltage, if possible. The intent of the “As Received”, no load, run test is to get the motor operating safely up to top speed for electrical characteristics, bearing temperature, and vibration checks prior to dissassembly. If the “As Received” motor conditions permit, the motor shall be run to 100% speed for these tests.
2.3 Disassemble & Inspection
A thorough appraisal of the motor’s condition, as received, is to be performed, to determine what specific repairs are needed as well as to find unsuspected trouble, perhaps unrelated to the obvious defect. Our technicians diagnose cause and effect to help prevent a recurrence. The motor may have been sent to our Repair Facility with limited external evidence as to the nature and location of trouble. What seems wrong may be correctable in several ways. Our appraisal will include a complete review of the following conditions of each part of the motor: General cleanliness, Cracked or broken welds or castings, Missing hardware, Wear or rub marks, including fretting, discoloration, charring, or other evidence of overheating, Looseness at mating fits, Corrosion, moisture, or oil inside the machine.
4.0 TEST STATOR WINDINGS
A full test of the winding condition shall be carried out with the motor disassembled. Windings are tested to ensure that there are no grounds, short circuits, open circuits, incorrect connections or high resistance connections. The condition of the windings and the extent of repairs should be determined by inspection and, as necessary, by tests. Bars and end rings for amortisseur and squirrel cage windings should be examined for evidence of defects. Testing may be needed. Winding data should be reviewed for accuracy. The Baker AWA 2.2 Advanced Winding Analyzer/Surge Test unit is to be used to carry out the following tests: 2.4.1.1 Winding Resistance and Inductance (Per IEEE 1415)
Winding resistance comparison tests (There shall be no more than 5% difference between the winding resistance readings)
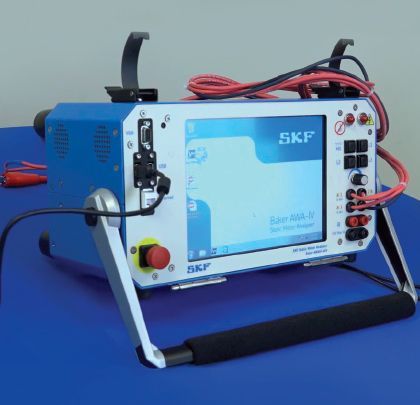
2.5 Mechanical Inspection
All mechanical parts are to be thoroughly cleaned and inspected for defects, cracks or damage at 44 points. Visually check for evidence of rubbing at outside diameters (fan, shrouds, end rings, armature laminations, etc.). If possible, a check is made for tightness of the core on its shaft. Visual inspection for signs of axial and radial movement are made. Visually check rotating components for excessive heating and other abnormalities, as well as an Inspection of condition of bar joints, end rings, windings, slip rings, key ways, threaded fits, synchronous pole pieces, etc. Furthermore, measure and record dimensions of the following: Shaft extension, Journal and bearing fits, Shaft extension runout, Shaft seal fits, Collector ring diameter, Brush size and type of quantity, as well as visually inspect the condition of non-rotating components (brackets, baffles, shrouds, brush holders, brushes, gasket, spacers, shims, threaded fits, machine fits, feet, etc.). and measure and record bracket fits for housings, cartridges, and bearings, the condition of ball or roller bearing housing or cartridges (wear, grooving, seal fits, fretting, grease fitting, insulation, oil gages, etc.),the condition of sleeve bearings while still in brackets (wear, oil grooves, oil rings, seals, insulation, seal fit, bracket ware, dowels, parts, etc.),stator laminations, mounting blocks, welds, machined fits, brush rigging, space heaters, etc., inspect rotor pole pieces, mounting blocks, amortisseur windings, leads, etc. Terminal boxes should accommodate the connections without crowding. Missing terminal boxes should be replaced, and damaged terminal boxes should be repaired or replaced. Gaskets and seals should be replaced where necessary. The fans and cooling ducts should be clean and operational. Cover plates and air baffles should be in place. Damaged or missing parts of the cooling system should be repaired or replaced. Any Damage appraisal of motor components is divided into two categories, electrical and mechanical.
6.0 STATOR REWINDING
Rewind the stator to a full Class “H” insulation specification. Ensure full slot wedges and full phase separation is included. Slot liners are installed for all motors. Coils are formed from continuous lengths of properly sized and insulated magnet wire (to match nameplate criteria). Insertion of coils in slots is done with extreme care to avoid damage to the insulation or magnet wire. Crossings of magnet wire within the slots should be held to a minimum on random-wound coils.
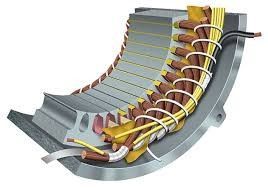
7.0 BALANCE ROTOR
EMX Shop Balancing Systems are designed to perform measurements of vibrations and calculations in horizontal shop balancing machines and in the field. The motor rotor shall be dynamically balanced in a balance stand before assembly of the motor. Rotors are supported at the bearing position. Ref EASA AR 100 Dynamic balancing of the rotating element should be to the level specified by the customer. In the absence of a requested level, dynamic balancing to balance quality grade G2.5 (ISO 1940/1) should enable the machine to meet final vibration limits.
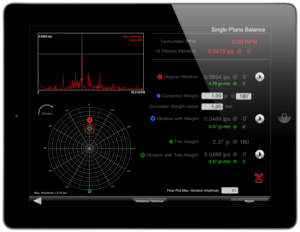
8.0 ASSEMBLE MOTOR
All Electric Motor assemblies are made in accordance with the equipment technical manual and good machine shop practices. All mechanical repairs on shafts, bearing journals, end bells, and other equipment are handled in-house by experienced machinists. Motors will be assembled in a manner that will ensure proper fit and alignment. Check and record air gap. The assembly of the motor is the reverse of the disassembly process and the following points shall be observed. All match marks shall line up. All assembled components will be checked to ensure secure fits.
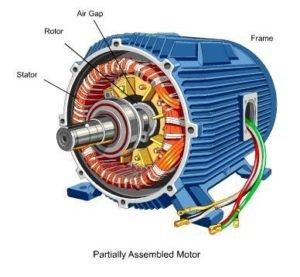
9.0 FINAL MOTOR TEST
After the insulation tests, the motor shall be run at no load at full terminal voltage, with either a half key or a half coupling, on the shaft. If the motor uses an external oil supply and removal system in normal use, a similar system shall be arranged for the test. The motor is to be run at nameplate voltage, frequency and speed. Record the no-load current drawn on all phases and document. Run test shall be a minimum of 45 minutes duration at the rated voltage and until the temperature of the bearings have stabilized (+/- 1°C over 15 minutes). On squirrel-cage motors, check the current on all connections and check speed of the motor. The current on each phase should be within 10% deviation between any two other phases. On wound rotor motors, apply full primary voltage to stator and with rotor circuit open for a non-rotational test. Rotor open circuit voltage and stator current is measured. A non-load test run will be made on all motors to ensure that all electrical readings do not exceed the Name Plate Data ratings. A written record of all tests and inspection results will be furnished to the user upon completion of repairs.
10.0 PAINT & PROTECTION
At the completion of the test, the motor shall be painted, unless otherwise requested by the customer, with two coats of EM Machinery Grey paint or Customer preferred paint color or type, and prepared for shipment. All motor products must be clean and free of any dirt, oil or grease on the primed surface prior to finish painting. Any lubricant and coolant inlets and outlets shall be plugged and masked before painting and shipping. Film thickness: 2 to 4 mils. The shaft shall be protected by either a rust and corrosion preventing coating or mechanical impact cover. A non-silicon rust inhibitor or light oil may also be applied to the shaft before shipping. Exposed machined surfaces (such as shaft extensions) should be coated with a rust-preventive coating unless the machine is to be returned to service immediately (The preferred coating is to spray Blue Layout Fluid from an aerosol can over the Motor Shaft and allow to dry a few minutes). Areas for vibration probes will be clean.
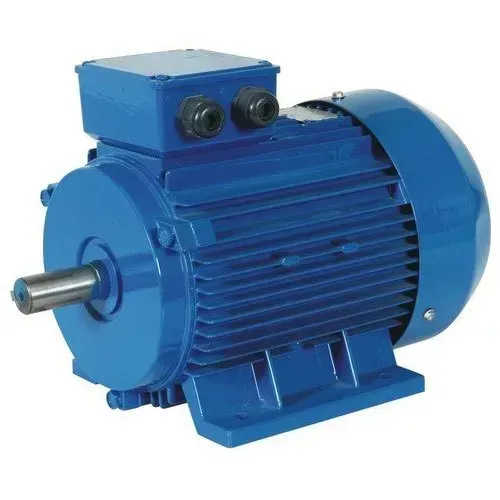
Rewind and Redesign
Rewind and Redesign-2 Year Warranty
MOTOR REWIND
Class “H” Insulation
Rewind the stator to a full Class “H” insulation specification.Ensure full slot wedges and full phase separation is included.Slot liners are installed for all motors. Coils are formed fromcontinuous lengths of properly sized and insulated magnet wire
ELECTRIC MOTOR REDESIGN
ELECTROMECHANEX has performed many successful redesigns for improved and longer lasting motor windings. Original motor designs (manufactured from 1950 to 1980) allow for modifications that can make repairs to your existing electric motor a better choice than buying a replacement.
The newer motor designs have improved insulation but typically run much hotter than the older original units do. This higher heat factor is directly related to the smaller motor sizes used today (to replace existing older motors). The main concern is that the newer motor designs might not have the same lifespan as the original units, which makes it worth considering the redesign option.
Our redesign offerings include:
- Voltage changes.
- Speed changes.
- Horsepower changes.
- Design improvements such as lower volts per turn and improved wire insulation.
- “Form coil” designs for improved insulation and longer life.
- Improved induction rotor designs (new bar and shorting rings).
- New M19/C5 lamination designs with laser-cut laminations for higher quality.
We know Motors! Contact us for a Motor Repair Quote, a Replacement Motor, or Predictive Maintenance Plans.
Winding Testing
Winding Testing and Analysis
AC Motors are tested using non-destructive winding analysis and testing and test run for proper electrical and mechanical operation. Voltage, Current, Bearing temperature, and Vibration are closely monitored and documented.
Every aspect of our AC Motor Repair shop, from electric motor rewinding to electric motor part repair, is performed under the stringent quality standards. As a reflection of our uncompromising commitment to customer satisfaction, all of EMX Electric Motors Service work is 100% guaranteed.
Root Cause Failure
Root Cause Failure Analysis
At Electromechanex, LLC we take pride in reliability engineering, isolating the root cause of the failure and repairing your motor to the highest possible standards and workmanship with the highest standard of reporting in the industry, as our intent is to let you know how to prevent the failure from happening again. As an EASA member, we serve as a total solutions provider for electrical and mechanical equipment and systems.
Specialty Motor Repair
Specialty Motor Repair
SPECIALTY MOTOR REPAIR
EMX Industrial Services can repair & recondition custom or specialty motor product, uncommon to standard motor manufacturing companies. We also provide in-house electric motor modification and customization, when there is a requirement for something different than a standard catalog motor. Our specialty work includes OEM Motors, Spindle Motors, Single Phase Motors, AC/DC Servo Motors, Motor/brake and Motor/pump combinations, Instant Reversal Speed Motors, and other special purpose electric motors by manufactures such as Demag, Eaton, Perske, Gusher,Grundfos,CEMP. The complexity of these motors lead customers to believe the motor is beyond repair. Allow us to perform diagnostic testing for you before a repair or replacement decision is made.
SPECIALTY MOTOR REPAIR
EMX Industrial Services can repair & recondition custom or specialty motor product, uncommon to standard motor manufacturing companies. We also provide in-house electric motor modification and customization, when there is a requirement for something different than a standard catalog motor. Our specialty work includes OEM Motors, Spindle Motors, Single Phase Motors, AC/DC Servo Motors, Motor/brake and Motor/pump combinations, Instant Reversal Speed Motors, and other special purpose electric motors by manufactures such as Demag, Eaton, Perske, Gusher,Grundfos,CEMP. The complexity of these motors lead customers to believe the motor is beyond repair. Allow us to perform diagnostic testing for you before a repair or replacement decision is made.
SPECIAL & CUSTOM MOTOR OF THE FOLLOWING DESIGNS
- Machine Tool
- Servo Motors
- Spindle Motors
- Brakemotors
- Crane and Hoist Motors
- Universal Electric motors
- Shunt motors
- Permanent magnet motors
- Flexible Shaft Motors
- Armature and Field Sets
- Agriculture
- Servo Drives
- Router Motors
- Shaker Duty
- Pumping Equipment
- Special purpose electric motors
- Custom Electric Motors
Got a Question? Contact us at (856) 362-4553 or email to service@electromechanex.com
Modification and Customization
Motor Modification and Customization
EMX provides in-house electric motor modification and customization, when there is a requirement for something different than a standard catalog motor. At times, finding the exact match to your motor need can be difficult. We provide service solutions that make it easy.Common requests include flange & bearing conversions and adapters, base modification, adding accessory items, etc. It is often more cost effective to purchase and modify a new motor to fit your application than it is to rewind the original motor. Often, greater efficiency and enhanced performance are also gained by replacement.
Mechanical
- Shaft Modification
- Diameter re-sizing: Reduction or increase of diameter.
- Splining, Re-keying, Add Flat
- Threading: Internal & External
- Special features
- Ball to roller or ceramic bearing conversion
- Adding encoders, tachometers
- Precision spec dynamic balancing
- Add Shaft Grounding Brushes
- Add Bearing Isolators
- Convert to C- Face, D-Flange & Custom Flange sizes
- Convert Motor with Foot to round body motor (steel band shells only)
- Chassis fabrication & modification
- Change Motor Paint Color, Special Environmental Coatings
Electrical
- Add winding or space heaters
- Adding PTs, Thermocouple, Bearing thermal & vibration sensors
- Install Terminal Block, Strip or panel in Junction Box
- Add Cord & Plug
SUPPORT CAPABILITIES TO BROAD RANGE OF INDUSTRIES
- Electric Power Utilities
- Agriculture
- Chemicals and Chemical Processing
- Glass Manufacturing
- Printing
- Commercial Properties
- Pulp and Paper
- Metals
- Food Processing Industries
- Plastics Manufacturing
- Mining & Earth Moving Operations
- Water and Waste Water (Municipal)